NORSOK Certified Polymer for Extreme Fire Protection
.
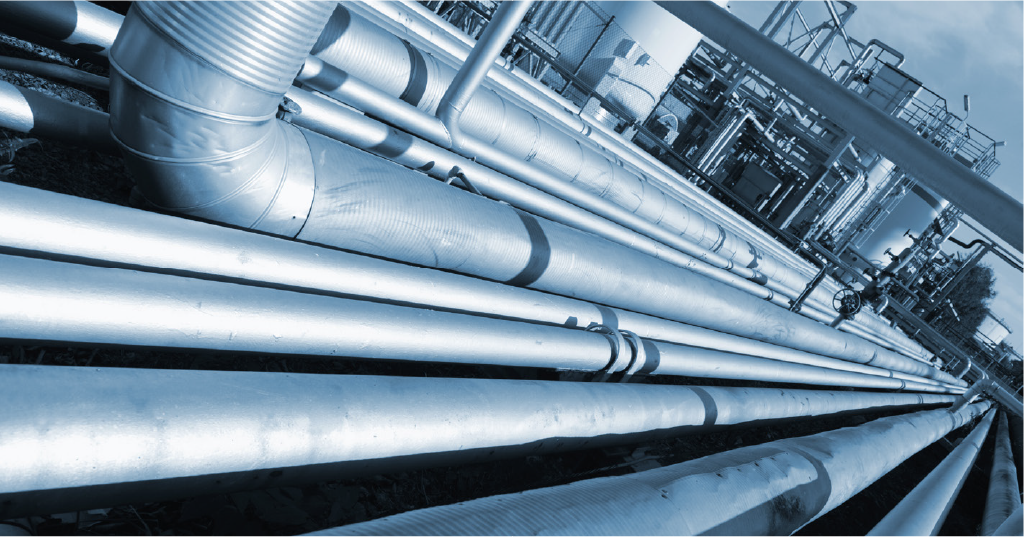
OGI sits down with Favuseal to learn more about NORSOK certified polymers, and Favuseal’s role in extreme fire protection. Favuseal AS is a Norwegian technology company that is currently supplying its technology to various companies that derive new innovative products and solutions superseding those currently found in the marketplace. We learn more below.
OGI: We have recently become aware of the fact that NORSOK has included Polymer-Based Fire Protection (PBFP) technology as a certified technology for extreme fire protection of offshore and land-based energy assets. Favuseal is a provider of PBFP. How was this achieved, and could you tell us a little bit more about the reasons why such a novel approach was taken by the NORSOK committee?
Favuseal: Favuseal is a Norwegian technology company that has dealt with fire protection since its inception. Several short comings compare to traditional epoxy-paint and fiber-based technologies was identified, and thru an extensive R&D and fire testing program the company came up with several new and innovative solutions to drive the innovation forward creating a paradigm shift in the passive fire protection industry. The fact that we managed to develop an ultra-slim flexible polymer that, when exposed to a fire, transforms itself away from being a polymer to a micro-porous ceramic state baffled some of the key stakeholders that we have been working with. The general idea was to develop a product with innovation height while being easy to install by certified installation companies around the world.
The vision of the company is to “Reduce the cost of high-performance passive fire protection Everywhere!”, and we purposely started with the toughest market of them all – the offshore market. Furthermore, we have been fortunate having several key stakeholders from Tier 1 energy companies onboard for quite some time. Without their input, we would never have been able to develop the solutions that are now commercially available in the marketplace. Without the guidance and input from NORSOK members, it could have gone very wrong numerous times! We firmly believe that the real trigger point of the committee member companies was the appealing attributes of the product offering back in the day where ultra-slim thicknesses, durability coupled with very appealing HSE attributes was the key trigger points of the NORSOK committee. Furthermore, the close collaboration that Favuseal has with EFECTIS, SWRI and RISE of Norway over many years also gave NORSOK validation how this technology would be beneficial to energy companies.
OGI: Can you explain to our readers what Polymer-Based Fire Protection actually does and how they are used in the energy sector?
Favuseal: Polymer-Based Fire Protection, or PBFP, is an ultra-thin flexible technology that utilizes two strong endothermic reaction processes to generate a stable micro-porous ceramic when exposed to a fire. The technology is not char forming as with paint-based technologies, but ceramifiable. The benefit is that the endothermic reaction processes are multi-directional, so it “cools off” the object it is protecting several times and in “every”direction. Moreover, the expansion of the technology is insignificant compared to e.g.epoxy-based or acrylic intumescent paint that expands some 600 – 1.000% from its original thickness. We felt like this fact is not conveyed properly to the marketplace, and might in many instances, pose as an inherent risk as the engineers might not have included room for this excessive expansion in their design. This fact was one of the shortcomings that we wanted to address.
The ultra-slim PBFP technology can be wrapped on to steel or GRE pipe work. Moreover, it is excellent for use on cables that needs to be upgraded to e.g. HC Pool fire, jet fire or high heat flux jet fire. The technology does not cause any ampacity changes when wrapped on to a single cable, or a bundle of cables. Any heat build-up from power cables is “vented” thru the technology and out in to the air.
Another very good example of an important stakeholder is the world’s largest cable company - Prysmian of Italy. Together with the Norwegian branch of Prysmian, we have jointly developed the world’s most robust cable portfolios that can withstand HC Pool fire, jet fires and even high heat flux jet fires. Commercially, these portfolios of cables are taken to the marketplace by Prysmian, but it goes without saying that we are very proud of the innovation height coming from the partnership with Prysmian. With respect to cables, the technology is extruded directly onto the cables via ordinary large extruders at high speeds. For the retrofit market, we have developed FavusealWrap-On:Cable – a solution that can be wrapped onto already installed cables to upgrade them to unprecedented levels of fire protection.
Another example of a long-term partnership is the one we are having with National Oilwell FGS where we work together to provide the marketplace with ultra-slim solutions that will live the lifetime of the asset it is protecting. The competence of NOV FGS when it comes to fire is unprecedented, and we look forward to further strengthening our relationship with them. Towards NOV FGS, we supply the technology on a roll for easy wrapping onto GRE pipework.
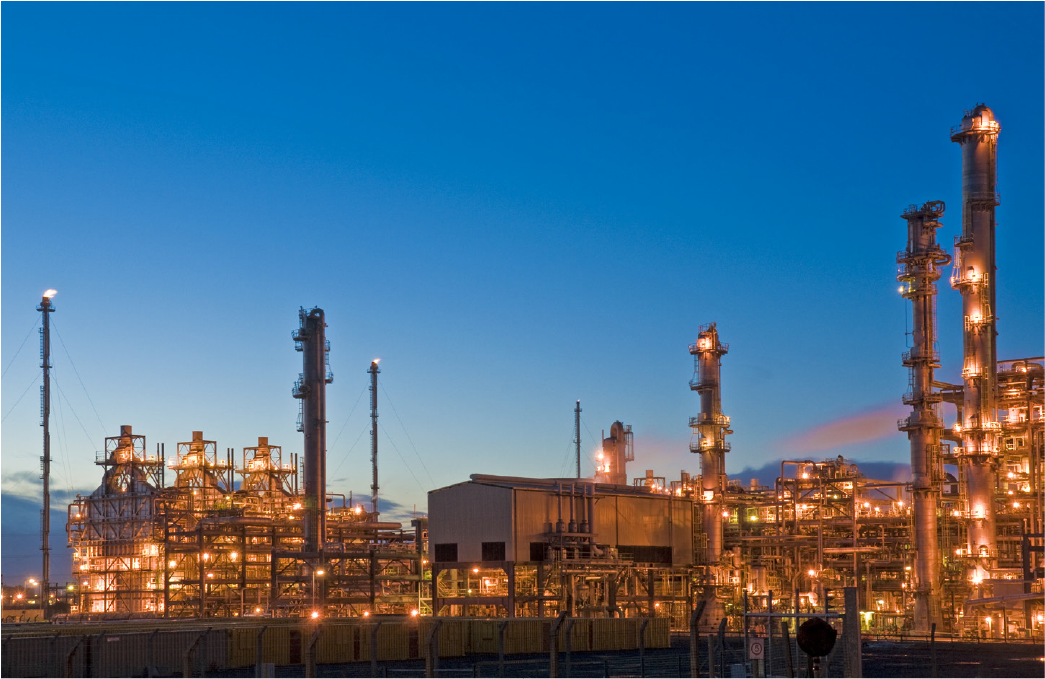
OGI: Are we to understand that you can simply just wrap the technology onto pipework? It sounds a bit too easy.
Favuseal: It is easy! However, you will need some sort of metal cladding to hold it into place when used on steel pipe work. However, this is not the case when we talk about GRE pipe work or safety critical cables.
OGI: How do you help companies increase their profits?
Favuseal: That is a difficult question to answer. It is strange providing passive fire protection solutions that you hope the end-client will never use. On the other hand, it is crucial that they work as intended and as per design if an accident occur. We have proven that PBFP technology has unchanged fire properties even after 15 years of service time offshore. The commercial benefit kicks in as time goes by as the solutions can be unwrapped and re-wrapped without the need of purchasing new products in case of inspection for corrosion under insulation (CUI). Furthermore, the need for maintenance is virtually a thing of the past if the installation is done properly. Based on experience, it is also clear that PBFP solutions will decrease clash points dramatically as the product offering is ultra-slim and does not expand outwards incase of a fire. I would estimate that the latter is a trigger for the asset owner as clash points are exceedingly costly when they occur. That, coupled with a very appealing HSE profile with no toxicity and no dust during installation makes a compelling argument for solutions based on PBFP technology.
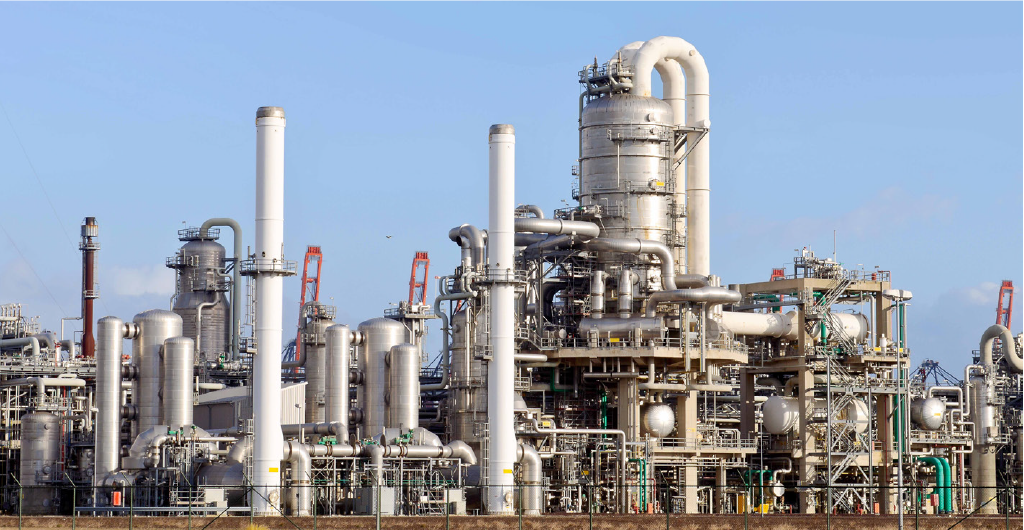
OGI: The environmental aspect is getting more and more important. How does Favuseal fit into that puzzle?
Favuseal: We are very proud of what we have achieved, and where we are going. Thru our licensed partner in Europe, we are producing PBFP technology utilizing a robotic manufacturing process. The consequence of this is that there is zero waste. The number of kilo input in raw materials equals the number of kilo output of finished products. The robotic manufacturing process overseen by 1 person allows for an output of more than 12 tons – per day – per shift! Together with our manufacturing partner, we are now also investigating if we can use renewable energy as input during the manufacturing of PBFP technology. We are committed to providing a zero-carbon footprint to our customers, and later this year, Favuseal will implement ISO-14001 in full. Per energy input via the grid, it is virtually impossible to generate as much Passive Fire Protection measured in m2 as is the case with PBFP technology. We firmly believe that we have a enormous responsibility towards our environment, and that we need to take care of it, and improve it, in order to leave a better planet to our children and future generations.
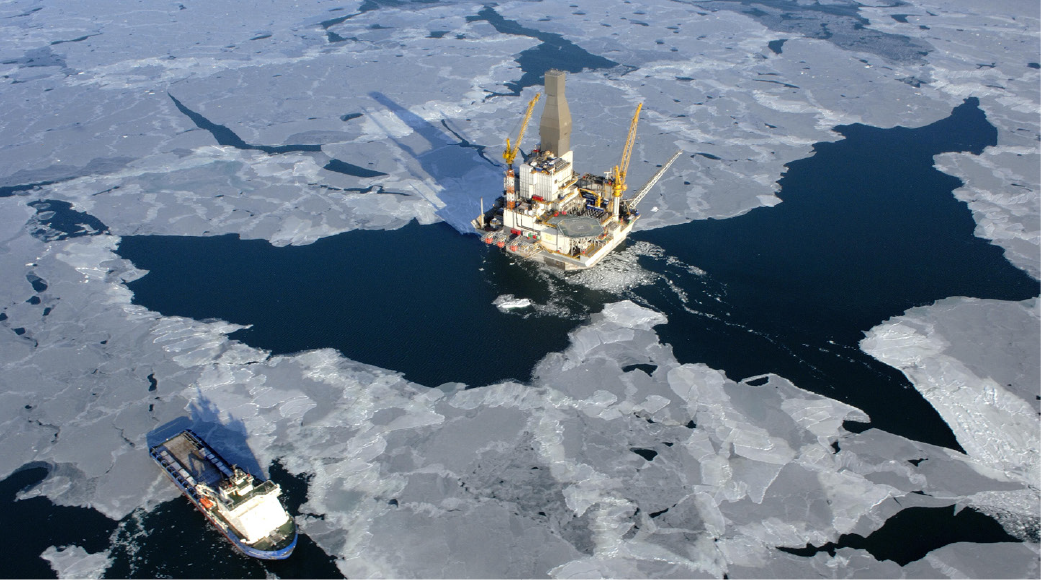
OGI: This all sounds impressive. Any plans for the future?
Favuseal: Later this year, we will commercially launch the TOTAL DESIGN INTEGRITY concept to the marketplace via reputable Tier 1 partners around the world. The TOTAL DESIGN INTEGRITY concept is a modular system that consist of building blocks that, when coupled together, will ensure the ongoing safety and integrity of the object it is protecting. All the products utilized in the concept will be derived from Polymer-Based Fire Protection technology. In sum, the concept will provide an ultra-slim solution that is non-expanding in case of a fire. The concept is tailor made to FPSO ́or other highly complex and dense energy assets such as nuclear plants that has extreme needs.
The concepts will be launched for safety critical cables and for GRE and steel pipework.
The TOTAL DESIGN INTEGRITY concepts are the sum, or culmination, of 10 years of collaboration with key industry players coupled with extensive R&D and fire testing. The main goal has been to take the pain out of doing passive fire protection via easy-to-install tested and approved modular ultra-slim solutions.
We are also very proud to tell you that these are not simply concepts. Favuseal have just recently completed the implementation of the TOTAL DESIGN INGERITY concept for both safety critical cables and steel pipework for a highly advanced FPSO. The feedback so far has been good due to the scalability in the execution phase and, more importantly, the dramatic reduction in clash points.
In conclusion, we really feel that we are value added to our customers and we will continue to work diligently to realize our vision of taking the pain out of doing passive fire protection while simultaneously reduce the cost associated with such products without compromising on integrity and our core company values.
OGI: Thank you for your time.
• Favuseal
E: admin@favuseal.com
W: www.favuseal.com
You might like these
Subscribe to our newsletter!
Subscribe to our newsletter to get the latest updates and insights from Favuseal.
By clicking submit you agree to the Terms and Conditions.
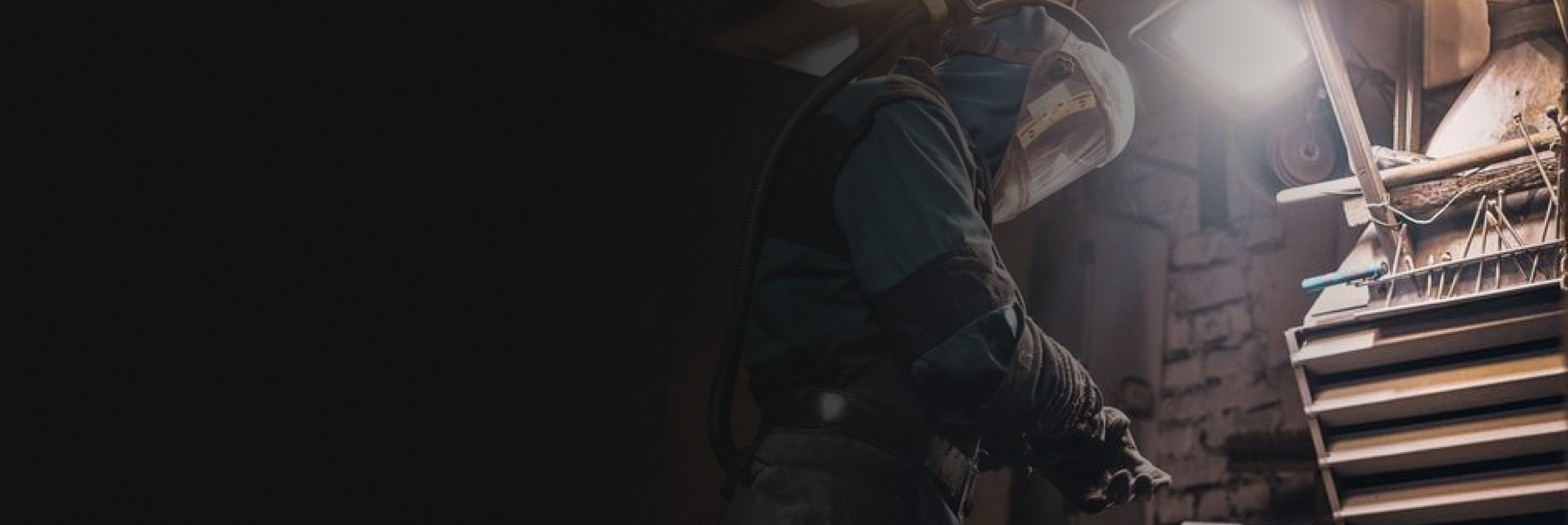
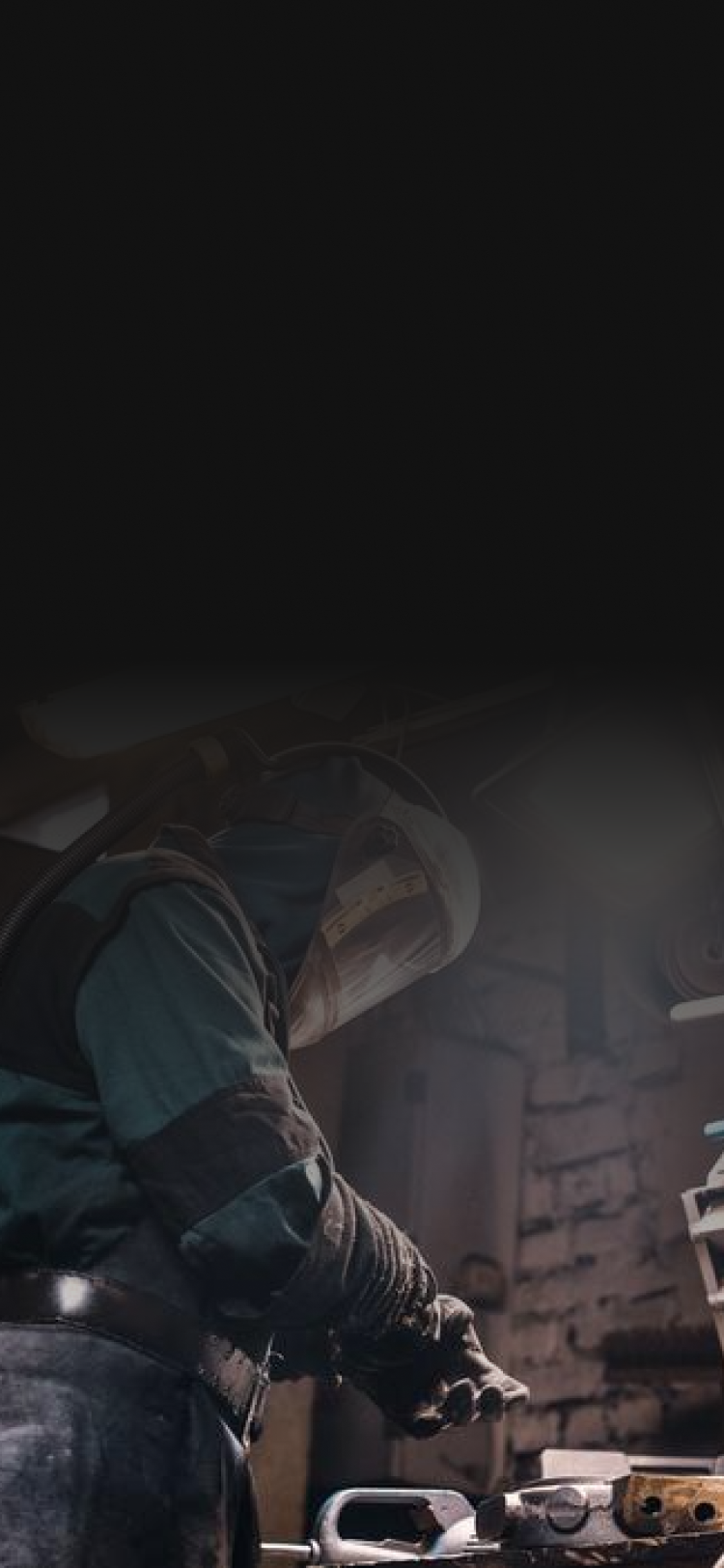